Desktop Metal

Desktop Metal's P50 printer, a machine I worked on during my time as a co-op
Desktop Metal exists to make metal 3D printing and carbon fiber 3D printing accessible to all engineers, designers, and manufacturers.
At Desktop Metal, I worked as a materials engineer co-op, working primarily with their binder jetting printers using various metals.
I supported the improvement of Desktop Metal’s binder jetting printing process with their selection of existing metal powders, as well as the development of new metal powders. From the project I worked on, I learned about system design, circuitry, and modeling, and learned a wide array of material characterization tests on different metal parts that were in development.

Maxiblend V-Blender
A V-blender is a machine used to homogenously mix dry powders.
Using a heated blender, metal powder can be conditioned by maintaining the powder at an elevated temperature, running gas through the body, and tumbling the powder at a set RPM to achieve desired specs.
At Desktop Metal, this machine was a key research and development tool in the powder conditioning process for use in binder jetting printers.
Two powders in a V-blender at 0 vs 9 revolutions
by Rocky DEM Particle Simulator
Project: V-Blender Upgrade
Problem: The previous iteration of the V-blender could not control its temperature autonomously, thus requiring manual operation of the heaters every minute over the course of 4-hour experiments. Temperature precision could only be reported within 5°C due to operator error.
Proposed Solution: Upgrade the V-blender into an autonomous machine, increase the precision of temperature control, and compile relevant information for future employee handoff and use.
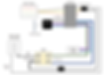.png)
Final Circuit Diagram
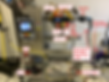.png)
Labeled Final V-Blender
.png)
Temperature Control System Flowchart
.jpg)
First Iteration Circuit Diagram
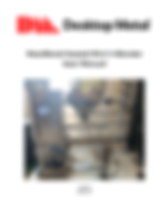.png)
User Manual for handoff
Actions:
-
Researched viable temperature control options, selecting PID as the ideal controller for 4-hour experiments operating at constant temperature
-
Created autonomous temperature control circuit using PID controller, thermocouple, and solid-state relay system
-
Created flowchart and circuit diagram for future employee use
-
-
Performed extensive testing for circuit safety and validated expected current readings using multimeter, incorporating additional safety features such as a current limiting fuse and relay heat sink
-
Designed and 3D printed custom electrical component mounts on V-blender body and on machine frame
-
Verified V-blender efficacy through extensive powder processing experiments
Results:
-
V-blender maintained set temperatures between 50 and 200°C for 12+ hours without manual operation or interference
-
V-blender maintained temperatures within 0.1°C precision
-
Created detailed user manual for future and current employee use, including electrical component details not previously documented