SharkNinja

SharkNinja's Flexstyle, a hairdryer/styler I worked on extensively to push to release
SharkNinja is a leading company in the consumer products industry; the Shark brand focuses on home improvement products, while the Ninja brand focuses on kitchenware products.
I worked as a Mechanical Engineering R&D co-op on the Shark Hair Care team that produces hairdryer and hairstyling appliances.
I supported the development of several hairdryer products in different phases of the design process. I gained stronger prototyping and problem solving skills, as well as DFM for air heaters and test development experience.

Project: Outlet Heat Uniformity Investigation
Problem: Third party CFD simulations on hairdryers found poor heat uniformity – air from certain regions were much hotter than other regions along the hairdryer outlet, which affects safety and hair styling ability. Air temperature should ideally be evenly distributed across the outlet.

Third Party CFD Simulation on Original Heater
Action:
-
Designed repeatable experiment to accurately and precisely measure air temperature and velocity along 4 axes across hair dryer outlet to verify CFD results on in-house units
-
Analyzed CFD and physical air temperature and velocity testing to diagnose the following:
-
Certain regions pre-outlet saw reduced air flow compared to other regions
-
Existing air flow did not draw sufficient heat due to heater geometry
-
Current outlet grille design created additional air pockets preventing air flow
-
-
Redesigned outlet grille to open air pocket
-
Designed several variations of baffle to redirect airflow to areas with poor flow
-
Designed several variations of the heater with different geometries to ensure even heat distribution, created early prototypes by modifying existing heaters
-
Created detailed CAD model of “ideal” heater with precise TCO, fuse, NTC, wiring and wiring connector locations. Sent to heater manufacturer with industry-standard engineering drawing for advanced prototype
Heater geometry is proprietary information. CAD images on the right are section views of heater to show non-proprietary features
Results:
-
Experiment designed to find temperature and velocity for uniformity investigation is now standard procedure to characterize all hair dryer units
-
Temperature and Velocity test results with first iteration prototypes of altered-geometry heater, baffle, and outlet grille informed decision for ideal heater-baffle-grille combination, in addition to third party CFD
-
Received fully functional, final prototype of “ideal” heater with necessary safety features from manufacturer based on CAD
-
Final prototype of “ideal” heater with new baffle and grille found drastically improved heat uniformity compared to original heater and to initial prototypes of new heater
-
Ongoing testing and implementation of new heater-baffle-grille
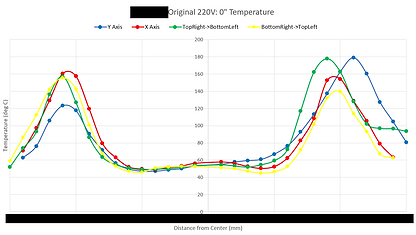
Measured Air Temperature Distribution

Final Ideal Heater CAD - NTC Terminals and Cutout

Final Ideal Heater CAD - TCO Section 1

Final Ideal Heater CAD - TCO Section 2

Final Ideal Heater CAD - Fuse Terminals

Original vs New Combination Final Results
Project: Venturi Flow Adapter

Problem: The current Venturi rig can only measure airflow from the outlet of a hair dryer with a room temperature air mode. Current competitor hot air brushes cannot be measured on the rig due to complex geometry and their lack of a true room temperature air mode, increasing static pressure of air. Create flow adapters to accurately measure airflow from a hot air brush on the Venturi rig.
Action:
-
Tested current competitor hot air brushes to verify “cool” mode emitting air temperatures of over 40°C, invalidating Venturi rig airflow due to heat
-
Designed flow adapter to measure room tem airflow into hot air brush inlet
-
Decided against measuring air temp from outlet to adjust for hot air pressure due to probe creating airflow turbulence and melting Venturi pipe
-
Room temperature inlet air minimizes impact of outlet heat on air pressure
-
Traded possible inaccuracy from power cord flow impedance for consistency between units at higher temperatures
-
-
Selected “clamshell” adapter design with two halves that enclose around handle of brush while sealing around power cord
-
Two halves split evenly to ensure sealing is along one axis
-
-
Adapter printed in multi-jet fusion HP PA-12 resin to achieve complex part geometry
-
Switched to closed-cell foam sealant form o-ring due to softer adapter material & lower clamping force
-
Groove depth designed for 60% reported compression of material
-
-
Screw bosses with heat set inserts designed to apply clamping force and align halves


Venturi Rig with Pipe Length L = 10*D for Fully Developed Flow
Clamshell Design with KF40 Interfacing Inlet to Seal onto Pipe
Groove Depth for 60% Compression - Draft Hole for Heat Set Insert

Adapter Set Up with Flexstyle (for testing purposes)

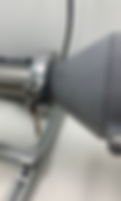
Adapter Clamp/Sealing System

Fully Sealed Adapter around Unit
Result:
-
Clamshell adapter measured airflow of hot air brush within 0.3 CFM, the reported Venturi rig imprecision, across several trials
-
Ultrasonic leak detector and smoke test verified negligible leakage from interface of two halves and around power cord
-
Clamshell adapter most effectively reduced effect of heat on airflow measurement compared to other methods
-
Measured < 0.3 CFM difference when measuring on “cool” vs “hot” mode using clamshell, measured > 1.0 difference when measuring airflow via unit outlet
-
-
Clamshell design easily re-printable and adjustable for future competitors
-
Clamshell adapter now standard procedure to measure airflow of any hot air brush
Project: Standard Characterization of New Products
Problem: SharkNinja is developing a new product that functions differently to previous products and previous KPIs and procedures do not accurately characterize the product. Determine KPIs and develop a standardized testing procedure for the new product.
Action:
-
Researched competitor products, consumer insights, and safety regulations with Product Development team to identify KPIs and associated target values
-
Employed DOE best practices to iterate and finalize procedures to measure KPIs with accuracy and precision
-
Created excel spreadsheets with macros to simplify data analyzation and detailed documentation for current and future employees to follow for consistent results after handoff
Results:
-
KPIs and procedures now standard practice to characterize new product and similar competitor products
-
Characterization tests informed important design changes to new product



New Product Test Procedures to Measure KPIs
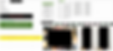
Spreadsheet to Read .csv and Analyze Raw Data